10 takeaways from Siderise’s first sustainability report
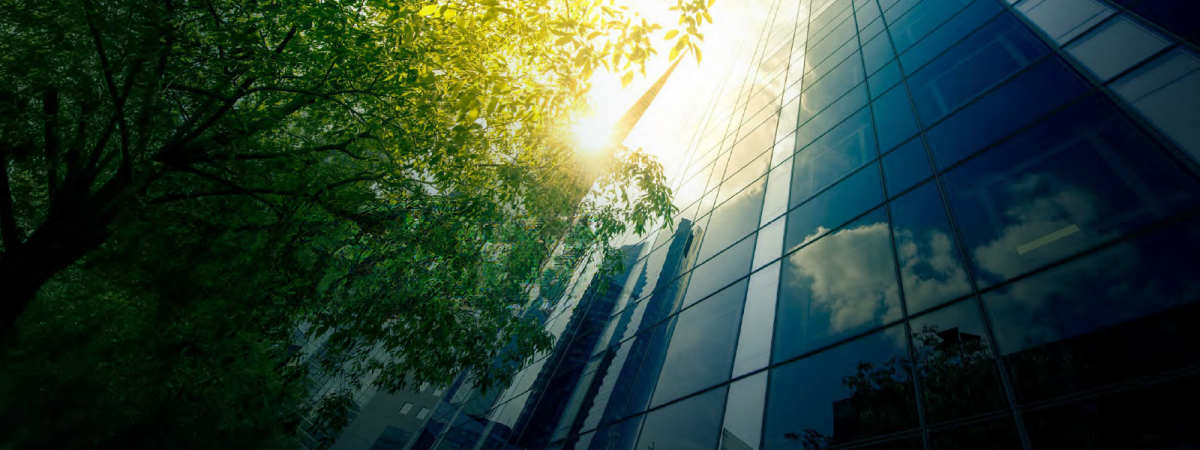
Our mission is ‘to go beyond, contributing to safer buildings.’ As well as creating high quality products that the market can rely on, a key part of this is also ensuring that our activities as a fast-growing global business do not have a negative impact on the environment around us and the communities in which we operate.
This is why, in 2023, we launched a clear Environmental, Social and Governance (ESG) strategy, consisting of four key pillars: Planet, People, Product, and Policy. Spearheaded by our Group ESG Manager, Sera Turkoglu, this journey first began by undertaking a materiality assessment which helped us highlight our critical areas of focus over the coming years. This looked at Siderise Group as whole, from our product quality and safety to our potential contributions to climate change. From here, we then set out to analyse our current position, make immediate positive changes where we could, and set out our short and medium term priorities.
To hold ourselves accountable and celebrate the significant milestones our teams have managed to hit already, we have created and published our first Sustainability Report.
Here are some of the key takeaways from this reporting period:
1. We’ve begun our journey to net zero scope 1 and 2 emissions
2023 marked the beginning of our ambitious goal to achieve net zero in GHG scope 1 and 2 emissions by 2030. We initiated this journey by assessing and identifying the key areas or ‘hot spots’ within our scope 1 and 2 emissions, laying the groundwork for targeted reductions through long-term solutions. Operating under the mantra of "reduce, produce, and procure," we implemented a multifaceted approach to drive emissions reductions, which included:
- Implementing energy-efficient lighting.
- Electrifying most of our forklift trucks.
- Transitioning to the purchasing of 100% renewable electricity at our Maesteg site.
- Transitioning our company cars to electric or hybrid models, with an aim to convert our entire fleet to 100% electric vehicles by 2030.
- Installing electric charging stations that are available for free use by both our employees and visitors.
We are also currently in the process of assessing a range of low or zero carbon technologies, such as solar PV and wind energy, with a target to produce 20% of our renewable energy onsite by 2030.
2. We’ve made progress in improving our waste management.
We’ve launched several projects aimed at improving waste management and reducing waste across our sites. This has included:
- Conducting site visits to our third-party waste management company facilities, to ensure compliance with contractual and legislative obligations.
- Introducing a waste segregation system in our offices and manufacturing areas to separate various streams, including paper / cardboard, plastic, metals, glass, food, and general waste.
- Scoping out a Lean Six Sigma project for optimising sheet sizes that aimed to decrease stone wool waste from our RH Horizontal ‘Open State’ Cavity Barrier manufacturing processes by 70% before recognising the potential for greater and more immediate reductions by prioritising our CW, EW and RV product range.
- Establishing a system to return stone wool waste from the manufacturing process back to our main stone wool supplier for recycling.
3. We’re exploring how recycled content can be used safely in our products and packaging
Linked to the above is our explorations into the possibilities of increasing the amount of recycled content within our products and packaging. Based on supplier information regarding the content of materials purchased, we estimate that our stone wool currently comprises approximately 25% indirect recycled content (as defined by ISO 14021. In addition to this, our primary supplier includes 8% direct recycled content generated via its production process. We are targeting 30% indirect recycled content in our primary product ranges by 2030 and are exploring the ways this can be achieved without impacting our product’s performance or certifications. Additionally, our cardboard packaging comprises 70% recycled materials, while our shrink pallet wrap consists of 30% recycled content.
4. We’ve started getting EPDs for our core product ranges
In 2023, we published our first third-party verified EPD for our RH Horizontal 'Open State' Cavity Barrier. Unlike traditional EPDs that focus solely on the environmental impacts during the manufacturing process i.e. ‘cradle-to-gate’, we're taking a ‘cradle-to-grave’ approach. This means that our Type III EPDs not only consider the environmental footprint of our products during production but also account for their end-of-life impacts. Our goal is to extend this initiative to all our core products, with the aim of having EPDs for each of them by 2025. By doing so, we are ensuring that our customers have access to comprehensive and transparent information about the environmental performance of our products, empowering them to make informed decisions that align with their sustainability goals.
5. We’re working with our supply chain to improve responsible sourcing
We believe that strong, collaborative relationships built on mutual trust and respect are essential for addressing ESG issues effectively. One key objective is to enhance transparency and traceability to ensure responsible sourcing and ethical business practices. By engaging in regular communication and dialogue with our suppliers, we can work together to identify challenges, share best practices, and drive continuous improvement in ESG performance. Plans are underway for the remainder of 2024 to incorporate social and environmental criteria into the supplier selection and periodic evaluation processes, and we are aiming to achieve BES 6001 responsible sourcing certification in 2024.
6. We’ve scaled up our commitment to continuous innovation
In March 2023, we opened our new £1.1m self-funded Innovation Centre at our headquarters in Maesteg. This provides us with the dedicated space and equipment to explore new materials, foster product development, and conduct rigorous testing of project-specific configurations and bespoke solutions. This has significantly increased our in-house testing capacity, with 126 tests conducted over the reporting period compared to 24 tests in 2022. Currently, we conduct up to 4 tests per week, each taking a day to complete, from construction to fire testing and demolition. Looking ahead, we are aiming to allocate 2% of turnover to R&D projects by 2025.
7. We’ve upgraded our quality control facilities
Both SIL and SSPL have been ISO 9001 certified since 2007, underscoring our longstanding commitment to excellence. However, following the publishing of the Independent Review of the Construction Product Testing Regime and its calls for manufacturers to take ownership of quality, we invested £200,000 into a state-of-the-art Quality Control Lab to ensure all our products offer outstanding performance. This not only facilitates off-the-line fire testing, but also comprehensive testing of raw materials before production. In August 2023, we also commissioned our new £2.1m high-speed automated production line— allowing us to increase production of our unique Lamella insulation by over 100%.
8. We’re investing heavily in internal training and competency assessments
We recognise that for customer and technical service to be accurate and accessible, it must be delivered by competent people. Job roles are assessed using a SKEB matrix (Skills, Knowledge, Experience and Behaviour) and our employees in customer facing roles undergo formalised training to ensure a baseline level of product knowledge, with ongoing upskilling for technical staff with a view to achieving professional qualifications provided by the Institution of Fire Engineers. 80% of employees in our UK offices are already considered fully trained and we are aiming to have 100% of staff who have been with us over six months to be classed as 100% trained by 2025.
9. We’re supporting our staff with upgrades to our health and wellbeing policies and resources
Safety remains our top priority, and we have intensified efforts in health and safety by investing in better KPI tracking and management systems. Beyond physical safety at work, we are also committed to protecting our employees’ wider well-being. In 2023, we commissioned Henley Reward Group to carry out an industry reward benchmarking exercise in the UK, reviewing our existing remuneration framework against those in both the locality and similar industries.
Following this, we implemented improvements including enhanced maternity and paternity pay and a maternity policy that includes a phased return on full pay. In addition to our employee assistance programme, we have also implemented a healthcare scheme providing employees and their families with 24/7 access to GPs. Our employee benefits platform also provides discounted gym membership and various tools supporting financial management.
10. Our people are getting out and making a difference in our local communities
In October 2023, we held our inaugural community engagement day. This was done in partnership with the Lost Peatlands of South Wales Project and Force for Nature. During this event, 13 of our employees planted 240 Sphagnum moss plants across a 10m2 area in Afan Forest Park, South Wales alongside other activities. This initiative aimed to restore the carbon capture and sink potential of local peat habitats. According to data published by the Woodland Trust, it is estimated that these efforts will result in the absorption of a total of 4.03 tons of carbon dioxide over the next 30 years.
We are looking to increase our community engagement initiatives both in the UK and in the wider regions we operate in, such as the UAE, India, US and Asia Pacific.
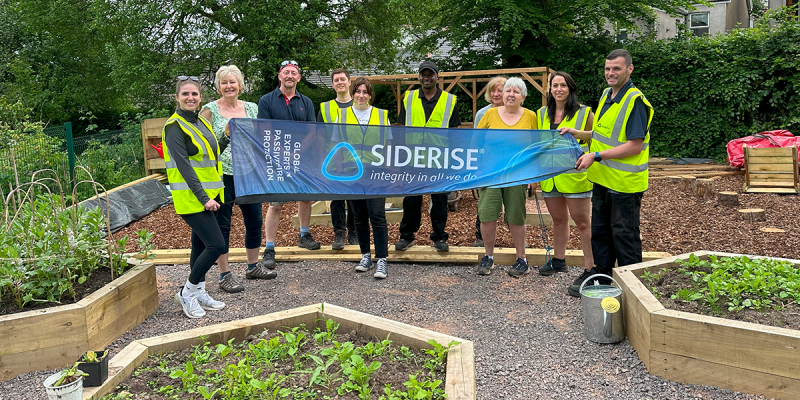
The next steps
We are incredibly proud of the leaps we have made in formalising our sustainability journey with huge amounts of progress made towards our 2024 and 2025 targets already. However, we know that this is a long-term commitment and fundamental to ensuring we live out our company values both now and far into the future. We are fully committed to not only investing in this vital work, but openly sharing our progress with our customers, suppliers and the wider industry.
Learn more about our ESG commitments and read our 2023 Sustainability Report in full here.
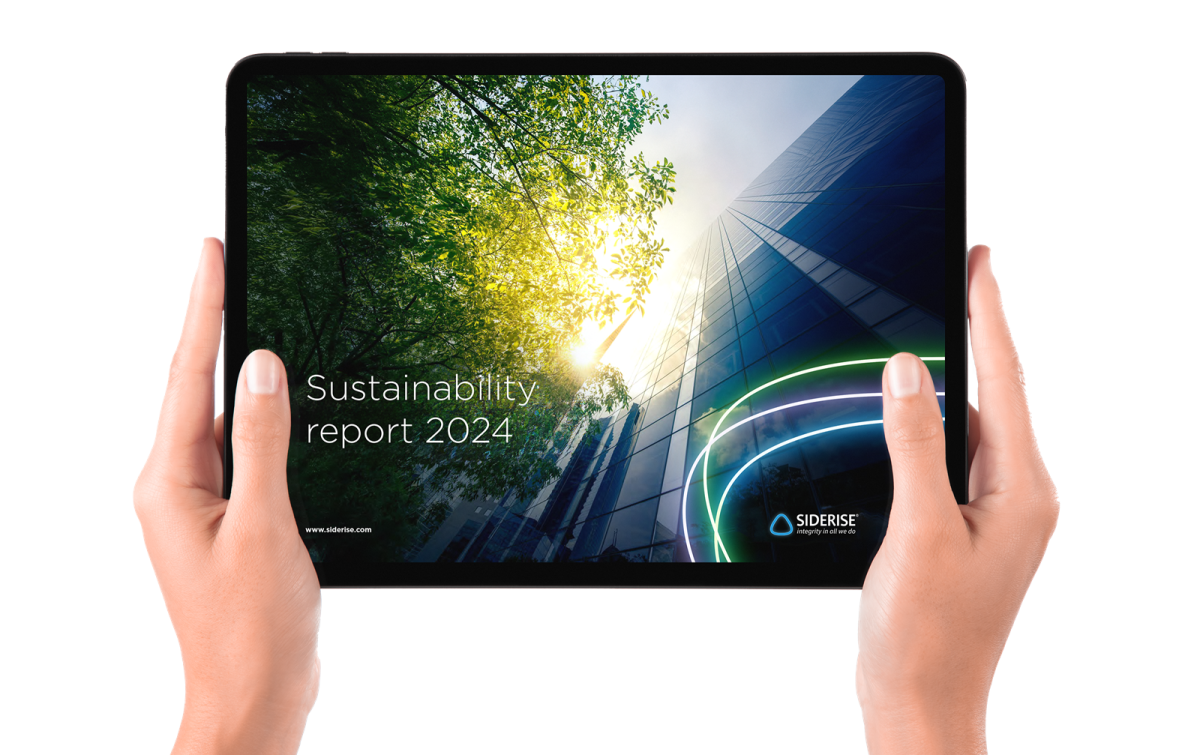