Remediating façades – contractor considerations for passive fire protection
Remediating cladding systems on ‘higher-risk buildings’ has become a key project stream for façade contractors across the UK. Whether these works require replacing the full system or addressing specific crucial elements, such as the passive fire protection, it is vital that project teams are not only well informed of the potential issues, but are supported to ensure effective compartmentation, compliance, and long-term safety.
The context of cladding remediation
Following the Grenfell Tower fire in 2017, widespread fire safety assessments of ‘higher risk’ buildings has led to thousands of properties being deemed unsafe and requiring remedial measures. These assessments involve conducting a Fire Risk Appraisal of External Walls (FRAEW), examining the cladding materials, fire test data and the quality of the passive fire protection installed in the façade system. However, progress through these works has been notoriously slow. Whilst 95% of buildings with the same type of cladding used on Grenfell have been remediated, only 30% of identified unsafe buildings in England alone have been remediated— with potentially thousands more yet to even be identified.
To tackle this, on 2nd December 2024, the government published its Remediation Acceleration Plan to increase the pace of identification and remediation for buildings in England with unsafe cladding, with clear target dates and harsher penalties for responsible parties who refuse to act. It aims to have all 18m+ (high-rise) buildings with unsafe cladding in a government-funded scheme remediated, and every 11m+ building with unsafe cladding remediated or at least have a date for completion by the end of 2029, otherwise landlords will be subject to legal action.
At the same time, the government shared its joint plan with developers to speed up their remediation strategies for the buildings they are responsible for. It states that “at least 29 developers, covering over 95% of the buildings which developers are remediating themselves, have committed to more than doubling the rate at which they have been assessing and starting to fix unsafe buildings, meaning work on all their buildings will start by summer 2027.”
In addition, building owners who fall outside government-funded remediation programs are also increasingly commissioning private fire risk assessments as a precautionary measure.
This all means that the pressure to remediate faster is intensifying and there is a growing demand for façade contractors who can demonstrate their knowledge of passive fire protection and have access to the right products and services.
Here are some of the key considerations for contractors working on these sensitive projects:
Common issues relating to passive fire protection
The effectiveness of passive fire protection in façades relies on high-quality installations. Issues that are commonly flagged when assessing existing projects that require urgent remediation include:
Lack of required cavity barriers or firestops
Incorrect orientation of firestops
Inadequate or absent brackets
Absence of positive retention to hold the intumescent on rainscreen open state cavity barriers in position
Incorrect fixings or tapes
Gaps between barriers and the inner leaf/outer leaf
Products with the wrong fire resistance levels
Incorrect product application for the size of air gaps
Poor firestopping around penetrations, e.g. pipes
Unapproved combinations of passive fire solutions with other systems
These problems could all result in an assembly which underperforms, potentially endangering both lives and property.
Of course, unless you are a specialist contractor, it can be a challenge to identify the exact nature of the issues, especially where there is an absence of detailed and representative drawings or design documentation from when the building was first constructed. At Siderise, we are increasingly being asked to go to sites, assess existing installations and provide our recommendations on the best approaches for a fire safe remediation. Once a strategy is decided upon, we can then help contracting teams to select the most appropriate products to remediate with, as well as quickly providing the necessary technical advice to help with technical details and drawings, and fire safety compliance information as well as site support to ensure an effective installation this time around.
Data supported product advice
Collaboration between contractors and manufacturers is vital for remediation projects, where working within the confines of existing building designs presents unique challenges. Not only are there numerous pre-existing materials to consider, but there may be design elements which are complex to protect retrospectively with standard passive fire protection solutions. For example, we recently worked on a remediation project which featured a curved facade element. We provided specification support and developed a bespoke passive fire protection solution to accommodate the curve.
We also commissioned and coordinated specific testing of the Siderise system and new façade panels to ensure they met the appropriate industry standards. Test data is key to accurate and compliant specifications. In addition to having access to an ever-growing bank of historic product testing data, we also have our own Innovation Centre and specialist fire test furnace that enables us to test products to any published fire test curve to BS, EN, ASTM, UL, and ISO standards. The Centre also carries UKAS accreditation to ISO 17025 - Testing and Calibration Laboratories. This verifies that it operates with technical competency and generates valid results.
Ensuring installation competence and quality assurance
The Building Safety Act makes clear that the competent use of products is a cornerstone of building safety, whilst the Building Safety Regulator (BSR) created by the Act, mandates competence for tradespeople in the construction industry. It is therefore vital that those undertaking cladding remediation have the right skills and knowledge to carry out the works.
Since installation contractors of passive fire protection systems are considered a ‘specialist trade, as a starting point there are several independent schemes that can include training, third-party certification, and professional qualifications. Whilst voluntary, they are good practice and help to ensure a strong foundation of competency. These often include various assessments of how projects are managed, how installations are carried out, and how they are overseen— in addition to annual audits and random site inspections. Depending on the schemes, they may also allow contractors to log their installations and issue certificates of conformity to the end client.
urers can also deliver product training to assist installers with evidencing and developing installation competence and provide invaluable insight into the specifics of their solutions, as well as how to address any potential build challenges to mitigate the risks of incorrect installation.
Siderise training blends classroom learning with practical learning to help installers of our passive fire protection products build their knowledge and understand how to correctly install these solutions. We are also an ASFP Recognised Training Provider. This verifies that our training offering is technically accurate, professionally presented, and both relevant and sufficient to demonstrate competence in passive fire protection (PFP). As such, these approved courses can also be used within the ASFP Competency Pathway, leading to the ASFP Pass Mark. Siderise are also a CITB Accredited Training organisation and will be developing training offers to meet with the National Occupational Standards under development
Learn more about our product training.
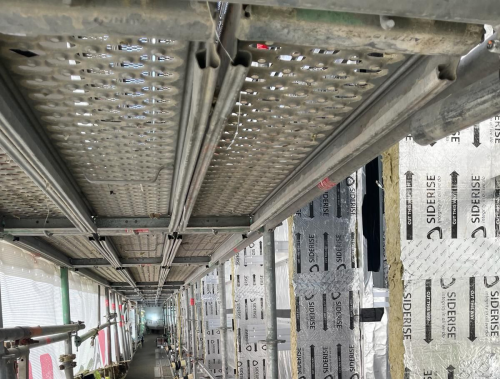
Supporting approval and maintaining the 'Golden Thread'
Often, issues with the passive fire protection installation can be missed, as Building Control inspections happen when the cavity barriers and firestops have been covered by the façade finish. To ensure remediation projects have been delivered to the highest levels of quality, making use of our free inspection service and planning regular checks—whether delivered in-person or via our dedicated Inspection App— can help to ensure that issues are identified and addressed and the works progress.
They also provide documentation which can be passed on to the building owner at the end of the project. This helps to maintain the ‘Golden Thread’ of product information and will be a useful reference point for any future modifications that may affect the building envelope. It can also be submitted as part of the evidence required for Gateway 3 to demonstrate that the building conforms with the regulatory requirements for firestopping.
Working together successfully
It is inescapable that cladding remediation projects will be a priority for the UK construction sector for a long time to come. To ensure the long-term safety of these buildings, contractors must engage in partnerships with passive fire protection manufacturers who provide more than just products. Specialist end-to-end technical support must include custom solutions for complex building designs, hands-on training, and rigorous inspection services.
Get in touch today to discuss how Siderise can support your remediation project requirements projects@siderise.com
Image courtesy of Thermoclad