Six ways specifiers can ensure accurate passive fire protection product specification
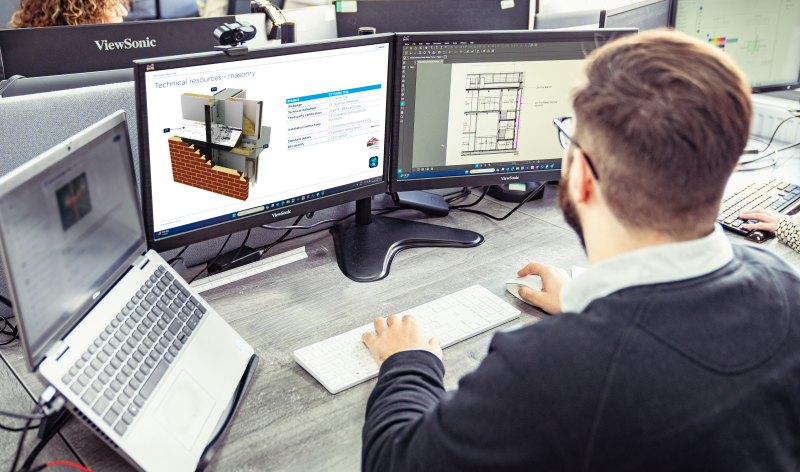
Wherever you are in the world, building safety relies on accurate product information. Without it, the risks of misguided specification or substitution, poor installation, inadequate classification, and noncompliance are high. This is especially prescient for passive fire protection, which is a fundamental but ultimately hidden part of an external wall system.
But how can specifiers and engineers ensure they are choosing the correct products for their project?
1. Validate product performance claims
Product misinformation is a key challenge for specifiers of building products. If performance claims have been incorrectly stated or understood, it can jeopardise the performance of the building as a whole, making it more likely to fall short of its aims, and may lead to non-compliance with Building Regulations or Codes. At best, this will incur additional costs and time to rectify the issues. At worst, inappropriate product selection can severely compromise a building’s safety and longevity, with potentially devastating consequences. One example of how this can happen is when manufacturers generalise product approvals across entire categories or ranges instead of defining exactly which products have been successfully tested to the relevant standard. For example, in the case of rainscreen façade cavity barriers, this could be specifying to the minimum and maximum voids that can be protected by each product and comparing the products’ integrity and insulation performance.
There are two ways that this risk can be mitigated. Firstly, specifiers should ensure the solutions they choose are supplied with all the relevant technical data sheets. Any performance claims should be backed up by testing that is relevant to the application it is intended for and carried out to the standards stipulated by the applicable compliance guidance or the regulations as a minimum. These results should be verified by accredited third-party certification bodies wherever possible as these schemes often include ongoing surveillance and auditing. This instils greater confidence in the manufacturer’s claims. Having this data easily accessible will allow engineers, other designers and auditing bodies working on the project to rigorously assess specifications, compare solutions and ensure compliance.
Whilst there are steps specifiers can take to verify claims, the onus is of course on the people who produce the products not to mislead. There is a clear and urgent need for greater transparency in the construction product market. Whilst some have been championing this approach for decades, taking steps to ensure their product data files are as comprehensive and transparent as possible, there is much more work to be done to ensure this approach is replicated across businesses and the industry globally.
One of the ways this is being driven at scale in the UK is through the Code for Construction Product Information (CCPI). This provides a benchmark for how product information is created, presented, and marketed by construction product manufacturers. It comprises 11 key clauses which have been designed to ensure product data is:
Clear
Accurate
Up-to-date
Accessible
Unambiguous.
This will allow everyone involved in specification and procurement to start from a level playing field, confident that the products they choose are not only suitable for the job in hand but have been subject to the appropriate tests and verifications.
Whilst this is a UK-focused scheme, its principles and approaches are clearly replicable across the world. All manufacturers, regardless of where they are selling their products, should not only be looking at the ways they verify and present their product data, but how they can explain this process to specifiers, offering reassurance that their products will support them in creating safe and compliant buildings.
2. Make use of digital design platforms
Digital design tools, such as BIM, are becoming common practice across the world as it not only helps facilitate easier cross-party collaboration and visualisation but also helps designers and specifiers to scrutinise the safety aspects of the design in greater detail. All this product data should therefore be captured within usable BIM models which have been authored to industry standards, such as the NBS BIM Object Standard, to allow for easy and accurate integration into digital models and designs and simple comparisons and analyses between objects that satisfy the standard.
In addition to this, information can also be hosted on specification platforms, such as NBS Source. This is a cloud-based platform that acts as a library of construction product information. This then integrates with NBS Chorus, which allows specifiers to create bespoke specifications and design models. To help with this process, Siderise’s NBS Chorus licence allows us to assist you with generating robust product specifications tailored to your project application as a licenced NBS Specification Writing Partner.
3. Collaborate with manufacturer technical departments
As experts in their products, manufacturers can assist with project-specific advice and guidance ranging from product selection advice and calculations to arranging bespoke testing of specific elements.
For example, some of the services we offer at Siderise are
Design feedback.
Technical datasheets and parameter guidance.
Example detail drawings and AR 3D visualisations.
Standard details of example façade arrangements.
Project specific product suitability advice.
Technical detail drawing reviews and overlays.
Method statements and sequencing information.
Mock-up constructions and product samples.
Project-specific testing at our UKAS-accredited test centre
Working with manufacturers of safety critical products earlier on in the construction process can help to limit the risk of changes to specifications as the products will not only be specified correctly for the application but be cost factored too. It can also help to build up a bank of information that can be incorporated in or used to contribute to the Golden Thread. This can include everything from test data to a history of technical communications and training and can be added to in later stages of construction, such as when product installation inspections have taken place.
4. Make the most of CPD and training opportunities
Understanding how product performance is measured and how a product should work can make it easier to spot inconsistencies and ensure that the correct test standards have been used. Undertaking CPD opportunities developed by passive fire protection experts is one way to enhance your knowledge and keep up to date with any technical advancements.
For example, at Siderise, we offer various training opportunities for specifiers working in all kinds of sectors and contexts such as:
CPD seminars in-person or livestream.
Webinars live and on-demand.
Online learning courses and educational e-modules.
ASFP Recognised product and application specific training programmes in-person at Siderise HQ.
National training roadshow events by invitation.
5. Check out the competency of your suppliers to provide this support
Of course, for manufacturers to be a genuinely useful resource, it is vital that the industry feels confident in their competency too. As a minimum, manufacturers should have some kind of independent verification of their quality control and management systems, such as ISO 9001. At Siderise, our laboratory facilitates off-the-line fire testing and comprehensive testing of raw materials before production to ensure our products offer outstanding performance. We also conduct stringent incoming checks on key materials from suppliers.
Additionally, manufacturers should also be making clear commitments to competency and upskilling. This is another thing requested by the CCPI, which states that anyone conveying ‘Product Information’ must be competent to the right level of knowledge.
For example, Siderise technical staff undergo formalised training with ongoing upskilling to ensure sufficient product knowledge, and with a view to achieving professional qualifications provided by the Institution of Fire Engineers (IFE). This ensures that design or product suitability advice is backed by accurate and accessible product data and has been delivered by someone competent enough to interpret the project needs and requirements, understand any potential parameters or limitations, and identify the right solutions.
6. Use Siderise Specification Packs
To support architects, fire engineers and specifiers in collating the rich technical data they need to ensure accurate and supported passive fire protection specifications, we have launched new Specification Packs. With versions available tailored to meet the needs of masonry, rainscreen, curtain wall, and precast and sealed external wall applications, each Specification Pack concisely summarises all the relevant product information for the designated application.
This includes:
Technical datasheets.
Third-party certification.
Standard detail drawings.
BIM objects.
Specification information and clauses.
Installation instructions.
It also introduces our enhanced support services available at different project stages. By including direct links to the latest information, users can be assured that they are working with the most up-to-date data and certifications, reducing risk of holding outdated material.
Contact us
We're here to help you
Call for our main switchboard
Email us for technical enquiries
Email us for site support
Complete the form for the right response