Remediating façades – contractor considerations for passive fire protection
Remediating cladding systems on ‘higher-risk buildings’ has become a key project stream for façade contractors across the UK. Whether these works require replacing the full system or addressing specific crucial elements, such as the passive fire protection, it is vital that project teams are not only well informed of the potential issues, but are supported to ensure effective compartmentation, compliance, and long-term safety.
The context of cladding remediation
Following the Grenfell Tower fire in 2017, widespread fire safety assessments of ‘higher risk’ buildings has led to thousands of properties being deemed unsafe and requiring remedial measures. These assessments involve conducting a Fire Risk Appraisal of External Walls (FRAEW), examining the cladding materials, fire test data and the quality of the passive fire protection installed in the façade system. However, progress through these works has been notoriously slow. Whilst 95% of buildings with the same type of cladding used on Grenfell have been remediated, only 30% of identified unsafe buildings in England alone have been remediated— with potentially thousands more yet to even be identified.
To tackle this, on 2nd December 2024, the government published its Remediation Acceleration Plan to increase the pace of identification and remediation for buildings in England with unsafe cladding, with clear target dates and harsher penalties for responsible parties who refuse to act. It aims to have all 18m+ (high-rise) buildings with unsafe cladding in a government-funded scheme remediated, and every 11m+ building with unsafe cladding remediated or at least have a date for completion by the end of 2029, otherwise landlords will be subject to legal action.
At the same time, the government shared its joint plan with developers to speed up their remediation strategies for the buildings they are responsible for. It states that “at least 29 developers, covering over 95% of the buildings which developers are remediating themselves, have committed to more than doubling the rate at which they have been assessing and starting to fix unsafe buildings, meaning work on all their buildings will start by summer 2027.”
In addition, building owners who fall outside government-funded remediation programs are also increasingly commissioning private fire risk assessments as a precautionary measure.
This all means that the pressure to remediate faster is intensifying and there is a growing demand for façade contractors who can demonstrate their knowledge of passive fire protection and have access to the right products and services.
Here are some of the key considerations for contractors working on these sensitive projects:
Common issues relating to passive fire protection
The effectiveness of passive fire protection in façades relies on high-quality installations. Issues that are commonly flagged when assessing existing projects that require urgent remediation include:
Lack of required cavity barriers or firestops
Incorrect orientation of firestops
Inadequate or absent brackets
Absence of positive retention to hold the intumescent on rainscreen open state cavity barriers in position
Incorrect fixings or tapes
Gaps between barriers and the inner leaf/outer leaf
Products with the wrong fire resistance levels
Incorrect product application for the size of air gaps
Poor firestopping around penetrations, e.g. pipes
Unapproved combinations of passive fire solutions with other systems
These problems could all result in an assembly which underperforms, potentially endangering both lives and property.
Of course, unless you are a specialist contractor, it can be a challenge to identify the exact nature of the issues, especially where there is an absence of detailed and representative drawings or design documentation from when the building was first constructed. At Siderise, we are increasingly being asked to go to sites, assess existing installations and provide our recommendations on the best approaches for a fire safe remediation. Once a strategy is decided upon, we can then help contracting teams to select the most appropriate products to remediate with, as well as quickly providing the necessary technical advice to help with technical details and drawings, and fire safety compliance information as well as site support to ensure an effective installation this time around.
Data supported product advice
Collaboration between contractors and manufacturers is vital for remediation projects, where working within the confines of existing building designs presents unique challenges. Not only are there numerous pre-existing materials to consider, but there may be design elements which are complex to protect retrospectively with standard passive fire protection solutions. For example, we recently worked on a remediation project which featured a curved facade element. We provided specification support and developed a bespoke passive fire protection solution to accommodate the curve.
We also commissioned and coordinated specific testing of the Siderise system and new façade panels to ensure they met the appropriate industry standards. Test data is key to accurate and compliant specifications. In addition to having access to an ever-growing bank of historic product testing data, we also have our own Innovation Centre and specialist fire test furnace that enables us to test products to any published fire test curve to BS, EN, ASTM, UL, and ISO standards. The Centre also carries UKAS accreditation to ISO 17025 - Testing and Calibration Laboratories. This verifies that it operates with technical competency and generates valid results.
Ensuring installation competence and quality assurance
The Building Safety Act makes clear that the competent use of products is a cornerstone of building safety, whilst the Building Safety Regulator (BSR) created by the Act, mandates competence for tradespeople in the construction industry. It is therefore vital that those undertaking cladding remediation have the right skills and knowledge to carry out the works.
Since installation contractors of passive fire protection systems are considered a ‘specialist trade, as a starting point there are several independent schemes that can include training, third-party certification, and professional qualifications. Whilst voluntary, they are good practice and help to ensure a strong foundation of competency. These often include various assessments of how projects are managed, how installations are carried out, and how they are overseen— in addition to annual audits and random site inspections. Depending on the schemes, they may also allow contractors to log their installations and issue certificates of conformity to the end client.
urers can also deliver product training to assist installers with evidencing and developing installation competence and provide invaluable insight into the specifics of their solutions, as well as how to address any potential build challenges to mitigate the risks of incorrect installation.
Siderise training blends classroom learning with practical learning to help installers of our passive fire protection products build their knowledge and understand how to correctly install these solutions. We are also an ASFP Recognised Training Provider. This verifies that our training offering is technically accurate, professionally presented, and both relevant and sufficient to demonstrate competence in passive fire protection (PFP). As such, these approved courses can also be used within the ASFP Competency Pathway, leading to the ASFP Pass Mark. Siderise are also a CITB Accredited Training organisation and will be developing training offers to meet with the National Occupational Standards under development
Supporting approval and maintaining the 'Golden Thread'
Often, issues with the passive fire protection installation can be missed, as Building Control inspections happen when the cavity barriers and firestops have been covered by the façade finish. To ensure remediation projects have been delivered to the highest levels of quality, making use of our free inspection service and planning regular checks—whether delivered in-person or via our dedicated Inspection App— can help to ensure that issues are identified and addressed and the works progress.
They also provide documentation which can be passed on to the building owner at the end of the project. This helps to maintain the ‘Golden Thread’ of product information and will be a useful reference point for any future modifications that may affect the building envelope. It can also be submitted as part of the evidence required for Gateway 3 to demonstrate that the building conforms with the regulatory requirements for firestopping.
Working together successfully
It is inescapable that cladding remediation projects will be a priority for the UK construction sector for a long time to come. To ensure the long-term safety of these buildings, contractors must engage in partnerships with passive fire protection manufacturers who provide more than just products. Specialist end-to-end technical support must include custom solutions for complex building designs, hands-on training, and rigorous inspection services.
Get in touch today to discuss how Siderise can support your remediation project requirements projects@siderise.com
Image courtesy of Thermoclad
Regional Façade Manager (North)
A year to remember – Siderise in 2024
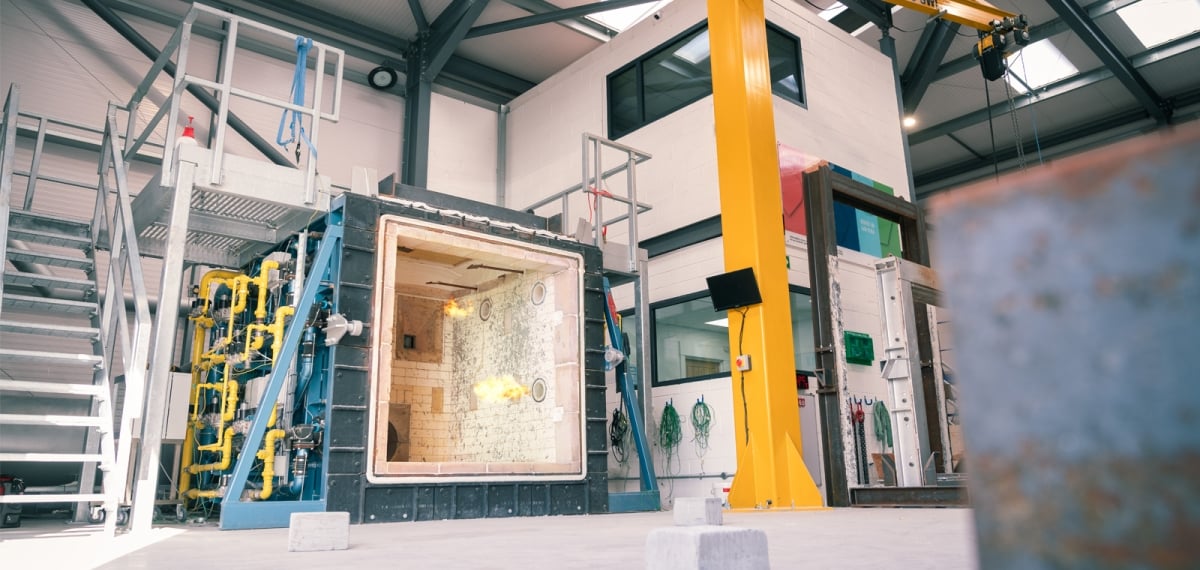
Working in the construction product industry has always brought endless opportunities for innovation, collaboration and development and, at Siderise, we’ve continually worked to put ourselves at the cutting edge of what’s new and what’s useful for our customers. However, in 2024, we have made significant strides in our mission to “Go Beyond, contributing to safer buildings.” Here are twelve of our most notable highlights from the last twelve months:
1. Getting our Innovation Centre UKAS-accredited
In July, we announced that our Innovation Centre at our Maesteg headquarters achieved UKAS ISO 17025 accreditation, validating that it operates with the highest technical competency and generates reliable results. We constructed the Innovation Centre to meet the increasing demand for testing and data for projects and product development and address a shortfall in available furnace time. From the outset, we knew we wanted to obtain UKAS accreditation to ensure we were operating it correctly to the international standard of competency. Gaining the accreditation was a rigorous process, with inspections of our Quality Management processes and records, and testing and training processes.
Learn more about our UKAS journey in our Q&A with our Director of Testing, Chris Mort.
2. Receiving CCPI Mark on all core passive fire protection product ranges
In November, we successfully completed the Code for Construction Product Information (CCPI) assessment process for:
RH Horizontal and RV Vertical Cavity Barrier for cladding applications
CT Cavity Tray and EW Cavity Barrier and Firestop for masonry external wall systems.
With approval already gained for the CW-FS Firestop range for curtain walling earlier in the year, this means all our main passive fire protection ranges now carry this best-practice mark, providing greater confidence that the information surrounding them is “clear, accurate, up-to-date, accessible and unambiguous.”
Read more about what the CCPI Mark signifies to our customers.
3. Being the first company to become an ASFP Recognised Training Provider
We were proud to be the first ASFP (Association for Specialist Fire Protection) Recognised Provider, independently verifying that our training offering is technically accurate, professionally presented, and both relevant and sufficient to demonstrate competence in passive fire protection. The new training recognition service provides independent third-party evaluation of training courses specific to passive fire protection (PFP). Once companies have demonstrated their approach to training quality and technical capability, their application is reviewed by an independent panel. All providers that meet this quality benchmark gain recognition from ASFP for training delivery and will be subject to ongoing oversight and quality monitoring. This ensures the industry has access to high quality training that is easily identifiable.
4. Delivering an industry-leading internal and external training offer
As highlighted above, we are extremely passionate about, and have invested a lot into, developing our training offering over the years. In 2024, we have really seen the value this is adding to our customers. From September 2023 – September 2024, our training team delivered 567 Product Information Training Sessions with 4,504 attendees! However, it is not only the high number of people attending the training that demonstrates its usefulness, but the feedback we have received explaining how our advice has enabled architects, fire engineers and contractors alike to work with greater confidence and insight.
Discover our training offering.
Linked to this is also our industry leading internal training programme. Since September 2023, 253 employees have participated in training sessions. A survey conducted as part of the company’s Sunday Times Best Places to Work 2024 assessment found that 83% of employees felt like they have enough information and training to do their job well.
5. Releasing our first Sustainability Report
At Siderise, we are driven by a bold mission: to go beyond, contributing to safer buildings. In addition to creating high quality products that the market can rely on, a key part of this is protecting the environment and communities around us. In October, we released our first annual Sustainability Report. This looks in detail at each of our four ESG strategy pillars— Planet, People, Product, and Policy— and outlines clear benchmarks in these crucial areas, identifying short and medium-term priorities that ensure business operations and ambitions align with recognised Sustainable Development Goals (SDGs).
6. Expanding our global footprint
We have been working to expand our global footprint and develop our regional teams, whilst staying true to our ethos of ‘integrity in all we do’ in both new and existing markets. For example, we have been working with our partners in the Middle East and India to set up a new facility, due to come online by the end of the year. which will allow us to hold stock locally to sell direct to customers and eventually begin manufacturing some products in the region. We’ve also been building our profile in the US, appointing a new Head of Commercial Brad Davis and adding several exciting projects to the pipeline. We have been testing our products to ASTM standards for years and have several solutions perfectly primed for this market. To accommodate our growing export market, we also expanded our warehouse facilities at Maesteg this year to store finished materials ready for timely distribution, which leads us to…
7. Completing some significant site upgrades— including a new production line and QC lab
In March, our new £2.1m high-speed automated production line went live — allowing us to increase production of our unique Lamella insulation by over 100%. Additionally, in response to recommendations of the Independent Review of the Construction Product Testing Regime, we built a £200,000 state-of-the-art Quality Control Lab to ensure our products offer outstanding performance. This not only facilitates off-the-line fire testing, but also comprehensive testing of raw materials before production.
To accommodate our growing headcount, we’ve also developed the office space at our Maesteg headquarters, including a £200,000 investment in creating new communal areas and installing electric vehicle charging points which are available free of charge to all visitors and employees.
8. Being named one of Sunday Times Best Places to Work 2024
The Sunday Times Best Places to Work 2024, powered by WorkL, is one of the most widely recognised and rigorously judged employment awards in the UK. So, we were over the moon to be listed in the Medium Business category, having received high scores across all questions and 87% of our employees stating that they feel proud to work for us and have a sense that they do something worthwhile by doing so.
As our CEO, Adam Turk, commented at the time: “At the start of 2023, we launched a new set of company values: Customer first, Safety matters, Integrity in all we do, Respect for each other, and Strive for betterment. Achieving this accolade on a national scale stands as testament to how well these values are already embedded into our workplace culture, and how integral they are to the future growth and success of the Siderise brand.”
9. Sharing our knowledge through useful engagement with the wider construction industry
We have continued to be actively involved in various industry associations and technical committees, and our experts have delivered various presentations at key sector events across the globe such as Zak World of Facades. Notably, CEO Adam Turk was announced as the Chair of the Construction Products Association (CPA) in April. With decades of experience across the construction industry, and having supported the CPA for over fifteen years, Adam is well placed to provide both leadership and insight to the CPA as it continues to represent and champion construction product manufacturers and suppliers in the UK.
Learn more about Adam’s vision for his chairmanship in the CPA’s press release.
10. Receiving award-winning recognition for our team’s hard work on local, national and industry stages
Whilst success is its own reward— especially where we’ve been able to add real value to our customers’ businesses—there’s nothing like being recognised by your peers. In October, we were proud to take home the trophy for Export Award at the Insider Media Made in Wales Awards— recognising our efforts to grow our global activities and champion Welsh manufacturing on the global stage. We were also shortlisted for Manufacturer of the Year— for which we were highly commended— and Innovation Award categories at the same award. We were also thrilled to be shortlisted for Building Awards Building’s Manufacturer of the Year after our win in 2023. As a business, we were also announced as finalists for the Culture Pioneers Awards in the Brand Category— showcasing how effectively our workplace culture reflects the ethos of our brand. Our work here was further underlined by winning the Construction Marketing Awards 2024 for ‘Best Stakeholder/Internal Communications’ for our Values campaign, delivered in collaboration with SLG Agency. This saw our core values developed into a visual representation to allow them to be effectively communicated to our growing employee base and embedded into our everyday operations.
11. Growing our digital offering through our new website and NBS partnership
We also launched our new website this year! In addition to offering an enhanced user experience on both desktop and mobile, the site is also intended to be a single source of truth for up-to-date product and system information. This is supported by robust test data, as well as dynamic features such as explorable 360° construction build-up renders, free interactive educational modules on key fire safety and acoustic topics with sign up options for more in-depth training. Linked to this is our investment in developing our specification tools to create comprehensive Specification Packs. For example, we are an NBS Source Partner and an NBS Chorus Specification Writing Partner. We are also in the process of developing our BIM models in light of feedback from our customers.
12. Working on some incredible projects!
This is what it is all about! Our products have been specified on some of the world’s most prestigious projects— and alongside our incredible distribution partners, it has been a privilege to work with some of the world’s best architects, developers, contractors and other manufacturers to ensure the highest standards of passive fire protection and acoustic performance.
Material planner
Head of Manufacturing
What is the difference between standard stone wool and lamella passive fire protection solutions?
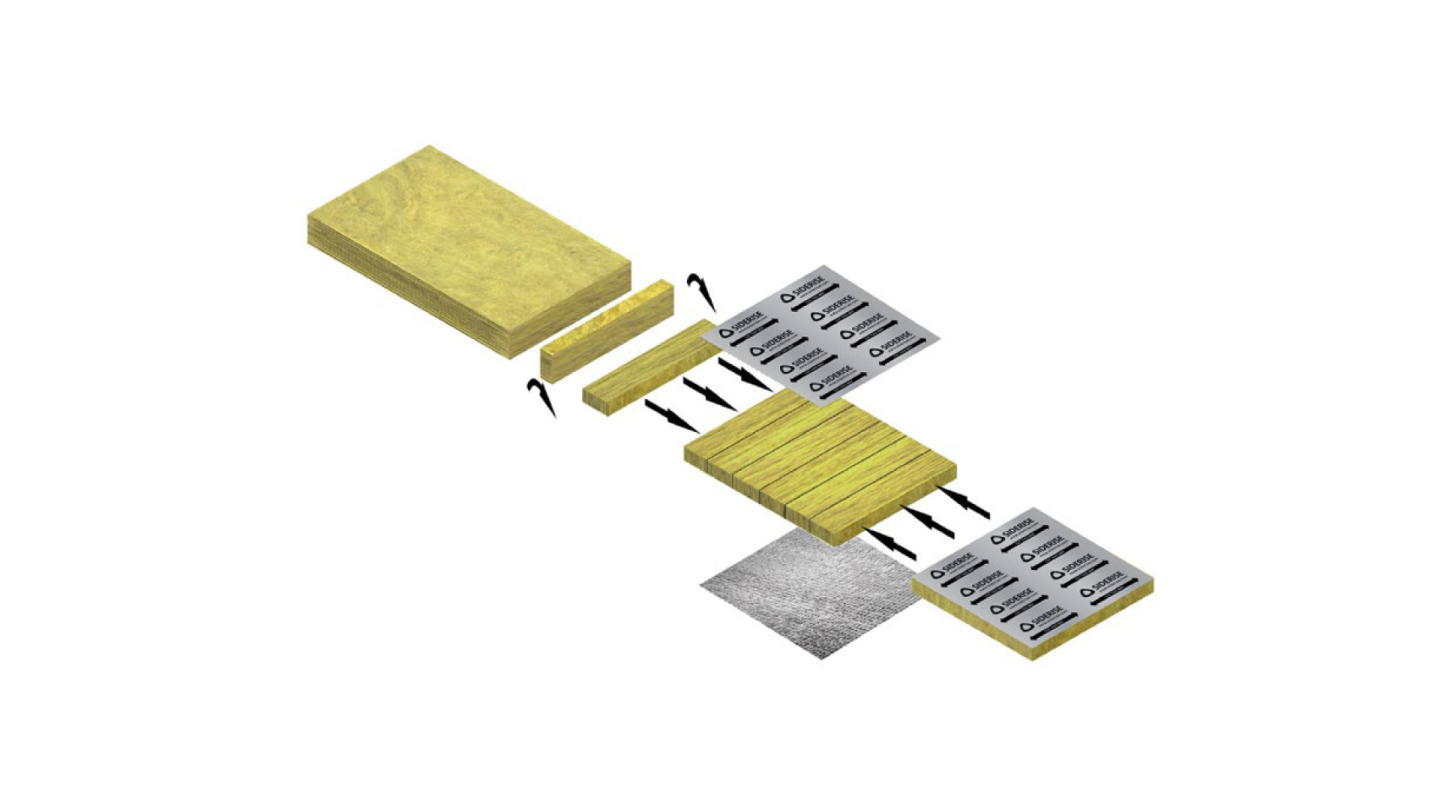
There are several different types of cavity barrier, firestop and perimeter seal solutions on the market developed for different façade types. These include curtain walling, rainscreen and composite cladding systems, precast concrete façades, and masonry walls. In all applications, it is vital that the chosen solution not only delivers the required fire resistance but also maintains the right level of compressibility and fit within the given void width for the lifetime of the system, even when subjected to building movement. Therefore, the durability and orientation of the stone wool fibres within the product is a key element in this functional performance.
Horizontal-fibred stone wool solutions
Standard passive fire protection products typically use non-combustible stone wool insulation with a horizontal fibre orientation. This makes the products stable but can equally make them resistant to lateral compression (across their width).
Continual exposure to movement and compression can result in breakdown of the bonding between the fibres, essentially ‘crushing’ them. This means that the product will not recover / flex in line with how the façade, inner leaf or floor slab is moving, which can result in a gap forming between the product and the façade over time, potentially causing the compartmentation provided by the cavity barrier, firestop or perimeter seal to fail prematurely.
In curtain wall applications, they also often require a ‘wet’ install, where installers cut and compress the insulation material onsite before sealing it with a sprayed-on compound. Once applied and cured, the only way to truly check the right compression has been achieved is through post-installation destructive testing.
Lamella (vertical-fibred) stone wool solutions
In response to the limitations presented by horizontally fibred products, Lamella products were engineered by us, here at Siderise. These feature a special formulation stone wool insulation with vertically oriented fibres, which are laterally compressed under quality-controlled factory conditions using a unique manufacturing process to assist with uniformity of product density, and remove any gaps between the adjoining cut sections, which may result in weakness.
This ‘pre-compression’ is held in place by heat-applying a foil facing to the cut face of the fibres, which also provides weather protection without the need for a wet sealant. When exposed to fire, this foil facing is sacrificed from the Lamella core, releasing the factory-induced compression. This allows the fibres to expand and ensure integrity is maintained - even under the movement caused by the fire load.
This unique and robust composition enables Lamella solutions to simply be friction fitted or installed with further compression of 10%, 20%, 5mm or 10mm with or without steel brackets, depending on factors such as the void width and façade type. What’s more, this additional compression wrinkles the foil, making it very easy to confirm if the product has been installed correctly without the need for destructive testing, unlike ‘wet-fit’ solutions.
As accelerated age testing in accordance with EOTA Technical Report 024 demonstrates, the Siderise vertical fibre structure allows our products to be repeatedly laterally compressed with no loss of recovery / flex. This gives them the ability to accommodate in-service movement, allowing the integrity of seal between the façade and floor slab / inner leaf to be constantly maintained for the lifetime of the building.
Robust options for long lasting building safety
Due to its resilient nature and practicality on site, Lamella now features in many of our passive fire protection and acoustic product ranges and has been used on projects around the world. Nonetheless, whichever solution is chosen, it is always important to ensure that the products have been thoroughly tested to standards relevant to their intended application and can demonstrate their suitability for that application.
Explore our passive fire protection products or check out our project case studies to learn more.
Contact us
We're here to help you
Call for our main switchboard
Email us for technical enquiries
Email us for site support
Complete the form for the right response
Keeping our rail industry on track – four key trends for UK rolling stock manufacturing and supplying in 2025
2025 marks 200 years since the opening of the Stockton and Darlington Railway— the world’s first public railway to use steam locomotives— putting the UK on the map for rail innovation. Since then, our railways have become a key part of everyday life, helping people and goods move across the country with ease. With this has come a huge investment in UK rolling stock capability, with some of the world’s biggest manufacturers setting up facilities in strategic locations.
However, there are multiple challenges facing the industry, from unstable procurement patterns to how to attract more passengers, to ensuring that our railways are ready to meet national decarbonisation goals. In this Insights piece, we explore some of the key trends and priorities for rolling stock manufacturers in the months ahead, and how our Noise Control division can support them.
Safety and quality
Ensuring the safety of passengers and staff will always be the utmost priority for any rolling stock manufacturer. In addition to ensuring the correct assembly and checking procedures are in place, a key part of this is making sure the products and materials used are code compliant and properly tested.
This is something which we are extremely passionate about at Siderise, and our testing capabilities have consistently set us apart from the competition. We have the ability to undertake small-scale acoustic and thermal testing in-house in our acoustics division and quality laboratory respectively. Our £1m Innovation Centre opened in Maesteg in 2023. This features a specialist furnace which allows our engineers to carry out fire-resistance testing in-house, bringing a huge benefit to our passive fire protection range in terms of research, development and quality control. We have also built strong relationships with external laboratories which can carry out larger-scale tests on materials where necessary.
In addition to working to extend its in-house testing capabilities, we are also always actively seeking to invest in third party accreditation. For example, one of our clients referenced the IRIS (International Railway Industry Standard) certification in their supplier onboarding process, so we have invested in proactively getting that accreditation in place before their production line comes on stream in the UK. Based on aerospace and automotive quality standards, IRIS Certification is a rigorous means of evaluating suppliers to the rail industry. To achieve it, organisations must demonstrate that they comply with ISO/TS 22163:2017 – and a range of other rules and procedures.
Customer comfort
The COVID pandemic obviously caused a huge drop in passenger numbers, and the industry has been steadily working to attract passengers back— with the latest Office for Rail and Road statistics demonstrating that revenue has grown to an estimated £1.6bn in the financial year 2023-2024. However, to not only get back up to the pre-pandemic £1.7bn of revenue, but beyond this, it is vital that the industry creates a positive and comfortable travel experience that convinces people to leave the car at home. A big part of this is considering carriage’s acoustic performance. Noise, both from surrounding activity and the train operation itself, can make train journeys hugely uncomfortable, especially for long journeys, and negate potential productivity benefits passengers can achieve travelling by rail as opposed to driving.
We often work closely with design teams to look at these issues and find ways to reduce noise using compliant insulation materials. Our in-house impedance tube test facility has proven particularly useful in these scenarios, allowing us to test acoustic absorption for small samples to ensure we have the correct solution in place before full size external testing is done.
Sustainability
As we move to a more sustainable way of life, we are seeing more hybrid drive systems coming to the market which offer flexibility and the option to change to electric/battery or hydrogen power in urban areas. We are also seeing an increase in the number of smaller regional train- and tramlines being revived as more and more cities look to encourage more people to use public transport instead of their cars.
From a product supplier perspective, this means we must ensure that we have solutions for all kinds of rolling stock, and they can deliver the comfort and reliability necessary. For instance, having the right insulation specification is not only crucial to keeping the interior at a desired temperature, but also helps to reduce energy consumption— a key consideration especially for the new battery powered trains. However, space is also often an important factor in cabin design. In these situations, it is important to ensure that the insulation material delivers a high enough thermal efficiency without compromising the thickness of the material and therefore negatively impacting on the available internal space for passengers. That’s why we offer a range of insulation options, with varying performance, thicknesses and weights.
Suppliers also need to be ready to keep up with evolving expectations as Environmental, Social and Governance (ESG) responsibilities gain greater attention in the rail sector. To demonstrate our commitment to ESG, we recently gained a silver EcoVadis rating with a score falling within the top five per cent globally. Ultimately, we aim to achieve a gold rating. You can learn more about our benchmarks and measures to integrate sustainable practice in our first Sustainability Report.
Collaboration
Of course, to address all these challenges, experts from across the sector need to be pooling their knowledge and expertise. For example, in the UK, over the last decade there has been a huge investment in the rail industry, with new rolling stock manufacturing facilities being built across the country. This has led to a lot of people migrating into the sector from other industries and from other countries, and Siderise has frequently been asked to share our experience and knowledge to help them to understand the materials, specifications and requirements necessary to deliver all kinds of specialist projects.
We’ve taken specifications that come from the other side of the world, analysed them in detail, and established that – while the material specification is safe to use – it has not been tested to European accreditation standards (for example EN 45545 Fire Protection on Railway Vehicles). So, we’ve then worked to understand the material and developed a bespoke product that meets the same performance criteria and then tested it to the relevant European standards— ensuring a locally-available product that ticks every box in terms of compliance, lower-carbon sourcing, shipping costs and lead times.
Siderise rail solutions
Siderise noise control treatments, HVAC solutions, and thermal insulation products have been keeping passengers safe and comfortable for over 25 years. In addition to providing our own range of products, which have been developed and tested over the years, we also have the capabilities to work with any client’s material specification to create bespoke solutions that meet their exacting needs. We can even look to ensure local sourcing of specialist materials where required, helping to save time and money for our customers.
But we don’t just see our role as a supplier of products. Siderise Group is passionate about supporting our customers— no matter the sector— with a suite of useful and accessible technical services. Seven people within our team are members of the Institute of Acoustics, and the business has extensive experience and a deep knowledge of passive fire protection.
Interested in learning more? Contact our dedicated acoustics team.
From design to build – helping you move best practice from Gateway 2 to Gateway 3
In our last two Insights pieces, we have explored the requirements of Gateway 2 and how manufacturers of safety-critical building products can provide support to project teams beyond the necessity of accurate product information. For instance, sharing their knowledge and experience to give specifiers a clear sense of ‘why’ a fire compartmentation product is suitable for the designated application and the ability to justify their decisions. However, passing through Gateway 2 is only the beginning.
Whilst Gateway 2 is designed to ensure that every detail of the construction is thoroughly planned and aligns with building regulations before any building work begins. However, to turn these safety-first plans into a reality, it is important that contracting teams have the support and resources necessary to both check and document that their installations are accurate and compliant with the specified designs and regulatory requirements, therefore allowing them to demonstrate a clear progression from Gateway 2 to completion at Gateway 3.
What is required at Gateway 3?
Like Gateway 2, Gateway 3 is another ‘hold point’ that occurs at the end of a project, once the construction works are complete. It requires the client, principal designer, and principal contractor to submit another application to the Building Safety Regulator (BSR) for a completion certificate. This application must demonstrate, with evidence, that the completed work reflects the approved plans and is therefore compliant with regulatory requirements, and that the construction has been carried out to a high standard by competent tradespersons — including signed compliance declarations from the principal designer and principal contractor confirming that they have fulfilled their duties under Part 2A of the Building Regulations.
Guidance documents such as ‘A Guide to Managing Safety-Critical Elements in Building Construction’, developed as a joint initiative between the Chartered Institute of Building (CIOB) and the Royal Institute of British Architects (RIBA) can be useful here. This Guide not only sets out a structured approach to the design, construction, and inspection of elements that specifically include firestopping and cavity barriers, but also gives examples of how to document evidence of compliance. These can include details of:
Benchmark constructions, samples, or mock-ups.
Toolbox talks, method statements and sequencing.
A robust log of detailed information, incorporating any manufacturer guidance, advice, and technical communications history that reflects any onsite changes,
Confirmation that cavity barrier and firestop installation operatives have undertaken appropriate product and application specific training.
Site works inspection reports with photographs of products to demonstrate that they have been correct installed before they are ‘closed in’.
The BSR then assesses the application and can carry out final inspections of the works. Once a project has passed through Gateway 3, it can then be registered with the BSR, the completion certificate issued, and the building deemed ready for occupation.
Why can building control inspection at this stage be a challenge for passive fire protection?
Final building control inspections are a crucial part of ensuring buildings reflect their designs in general. However, by the time these are undertaken, the passive fire protection elements of the building envelope will be concealed by the façade. Whilst on some projects, elements of the finished façade can be removed to check that cavity barriers and firestops have been installed correctly, this is not always possible depending on the façade type and how it is constructed. Also, these ‘spot checks’ don’t allow installation teams to demonstrate consistently high standards across the build— an important factor when looking at large projects such as high-rise buildings.
How can Siderise inspection services support Gateway 3 applications?
In addition to the support we offer for Gateway 2 applications (as explained in our earlier Insights’ pieces on the requirements and common queries), we offer a free inspection service to verify if Siderise products are installed in accordance with our installation guidance to ensure that they will perform as expected in the event of a fire. These inspections can form an integral part of the contractor’s overarching inspection plans and help them to demonstrate due diligence.
Our site inspections can be carried out either in-person, with periodic visits and support from our trained and experienced site services engineers or via the Siderise Inspection App that offers a straightforward photographic recording process
This digital form of inspection is suitable for checking the installation quality of our standard passive fire protection and acoustic systems as the programme progresses. It allows users to capture images as each area / element is being installed and to update the data input fields using their smartphone or tablet. The app then immediately turns this into a comprehensive, easy-to-understand report which can be reviewed offsite by a technical team to confirm the installation meets recommendations and to quickly identify if any areas need remedial actions before the works progress further preventing errors from being built in and helping to save time and money, whilst ensuring a consistently accurate installation across the project.
The reports from this collaborative service can be shared instantly with other project stakeholders and included in the Gateway 3 application and subsequent handover information, providing a clear digital record of exactly what’s in the building and how it was installed for traceability purposes. This helps to maintain that vital ‘Golden Thread’ of product information, support Building Control in ensuring the passive fire safety measures have been delivered correctly and can be a useful reference point for any future modifications to the project that may affect the building envelope.
Learn more about our comprehensive technical services or contact our Fire Safety Technical Services team to discuss getting your project through the Gateways via the contact form below or email technical.services@siderise.com.
Want to find out more?
Read our other Gateway 2 blog here: Supporting Gateway 2 applications and beyond – answering common queries | Siderise
Siderise RS Series Fixing Bracket Pre-drilled
Pre-drilled supporting bracket with a split end for use in the installation of Siderise RH Rainscreen Horizontal Open State Cavity Barrier. Available in a range of lengths to suit the required void size, and in stainless steel and galvanised steel variants to suit project specific requirements.
IMPORTANT NOTE - Pre-drilled brackets will be phased in throughout the remainder of 2024, with our current bracket offering expecting to be fully phased out by early 2025.
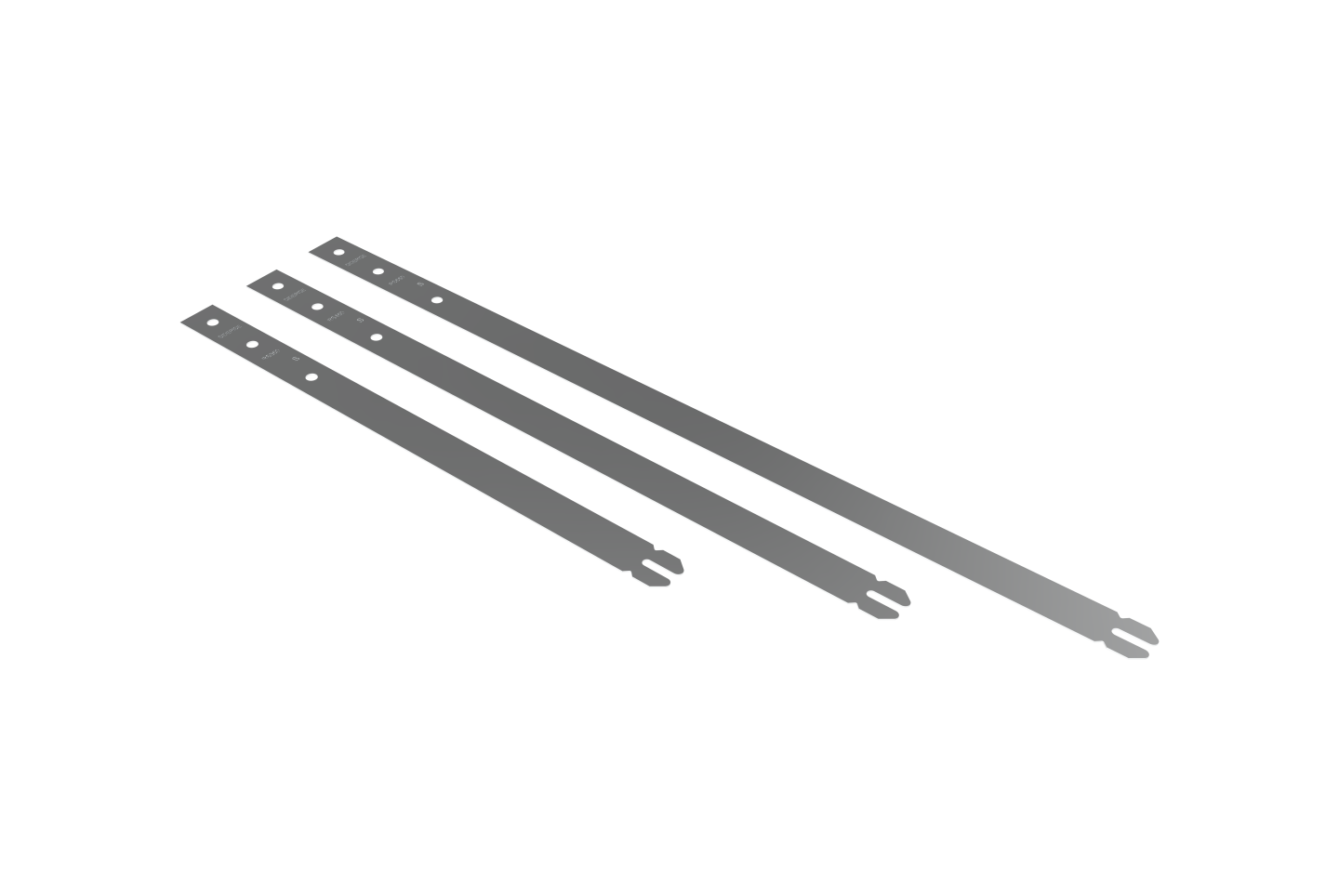
Developed specifically for Siderise Rainscreen OSCBs
Siderise RS Series Fixing Bracket provides secure and positive full penetration, mechanical retention for our RH Rainscreen Horizontal Open State Cavity Barriers, and is a requirement as part of the tested and third-party certified systems. With a 25mm width, RS series brackets are supplied in a range of lengths with three drill holes for fixing position versatility. The 7mm pre-drilled holes are designed to help facilitate a faster and simpler installation compared to brackets that require on-site drilling. In addition, the fixed length of the split end eliminates the need to cut to size onsite, while the notch feature aims to make the bending process easier.
For application specific information, see technical datasheet, installation instructions and standard details on the RH Rainscreen Horizontal Open State Cavity Barrier product page. https://www.siderise.com/fire-safety/cladding/rh/cavity-barriers-ventilated-cladding-rainscreen-horizontal
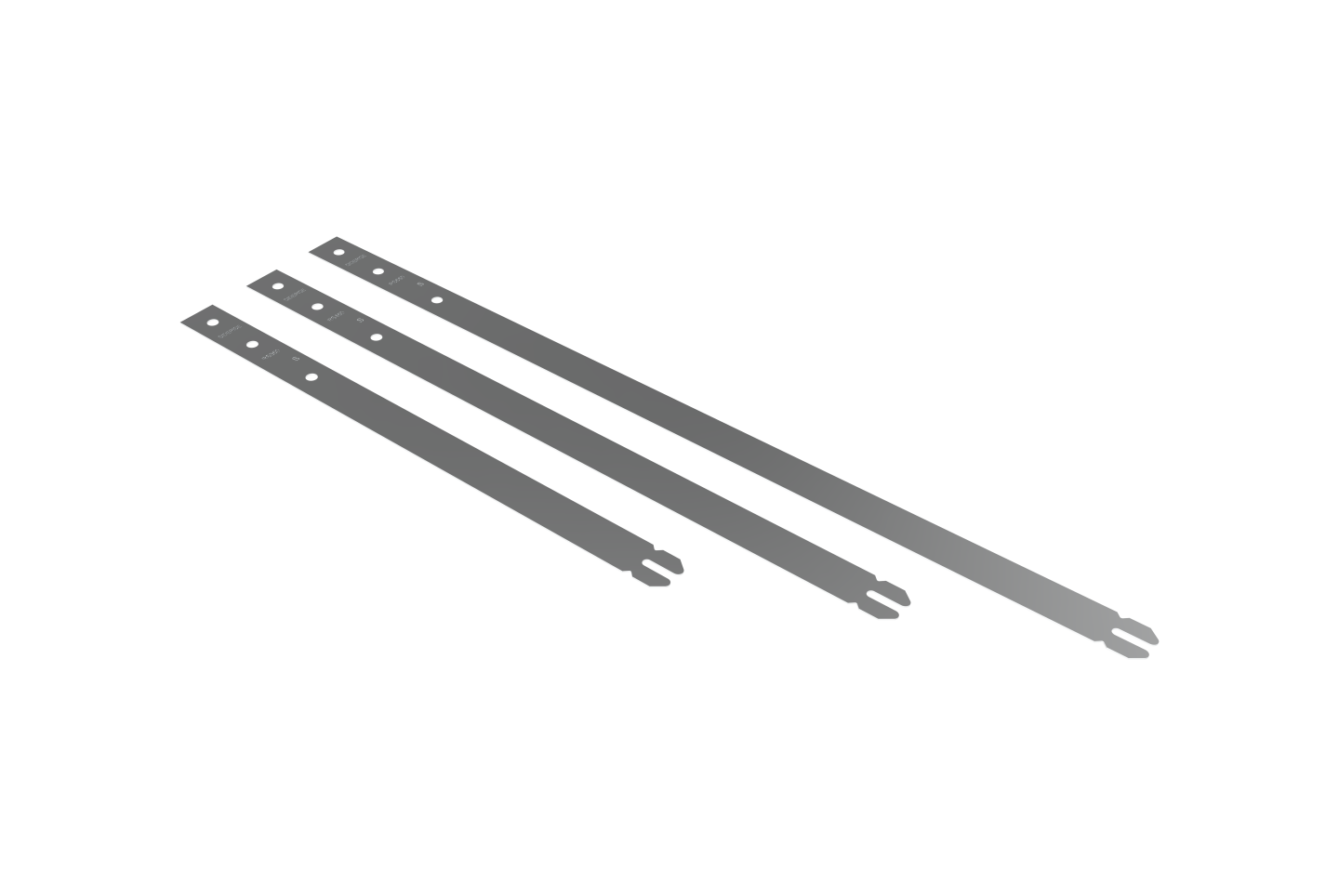
Siderise RS Series brackets are designed for quick and easy installation of specified Siderise products to supported system interfaces. RS series brackets are currently supplied for installation with Siderise open-state cavity barrier products such as RH & EWI. Please refer to each individual product technical datasheet and installation instructions to ascertain the correct bracket specification for the application and void dimensions on your project.
Table1: Bracket Dimensions
Product Ref. | Length(mm) | Width (mm) | Thickness Galv(mm) | Thickness SS(mm) |
---|---|---|---|---|
RS350 | 355 | 25 | 1.0 | 0.9 |
RS450 | 450 | 25 | 1.5 | 1.5 |
RS550 | 550 | 25 | 1.5 | 1.5 |
Please note: Length of bracket provided is measured in flat form from tip to tip.
Table 2: Pre -Galvanised Mild Steel Properties
Properties | Value |
---|---|
Description | Pre-Galvanised Mild Steel Brackets |
Grade | DX51-D |
Coating Weight | Z275 Zinc (Min Av triple spot coating mas g/m2) |
General Characteristics | Hot Dip Galvanised giving sacrificial protection to all areas after forming and fabrication |
Dimensional Tolerances | General: ±1.00mm |±2.0º |
Table 3: Stainless Steel Grade 304 Bracket Properties
Properties | Value |
---|---|
Description | Stainless Steel Brackets |
Grade | 304 |
General Characteristics | Widely used stainless chromium-nickel steels. General purpose grades with good resistance to atmospheric corrosion and many organic and inorganic chemicals |
Dimensional Tolerances | General: ±1.00mm |±2.0º |
Note: Stainless steel 316 grade available subject to minimum order quantity. Please contact our customer service team: customer.service@siderise.com for more information.
For technical advice or support please contact: technical.services@siderise.com
For Installation Training or Site Inspections please contact: site.services@siderise.com
For technical advice or support in the Middle East, India or Asia Pacific contact: smetech@siderise.com
The information in this datasheet is believed to be accurate at the date of publication. Siderise has a policy of continuous product improvement and reserves the right to alter or amend the specifications of products without prior notice. Siderise does not accept responsibility for the consequences of using the products described outside of the recommendations within this datasheet. Expert advice should be sought where there is any doubt about the correct specification or installation of Siderise products.
Augmented Reality
Point your camera at the QR code. Tap the banner that appears on your screen.
Siderise B Series Fixing Bracket Pre-drilled
Pre-drilled supporting bracket for use in the installation of Siderise cavity barriers and firestops. Available in a range of lengths to suit the required void size, and in stainless steel and galvanised steel variants to suit project specific requirements.
IMPORTANT NOTE - Pre-drilled brackets will be phased in throughout the remainder of 2024, with our current bracket offering expecting to be fully phased out by early 2025.
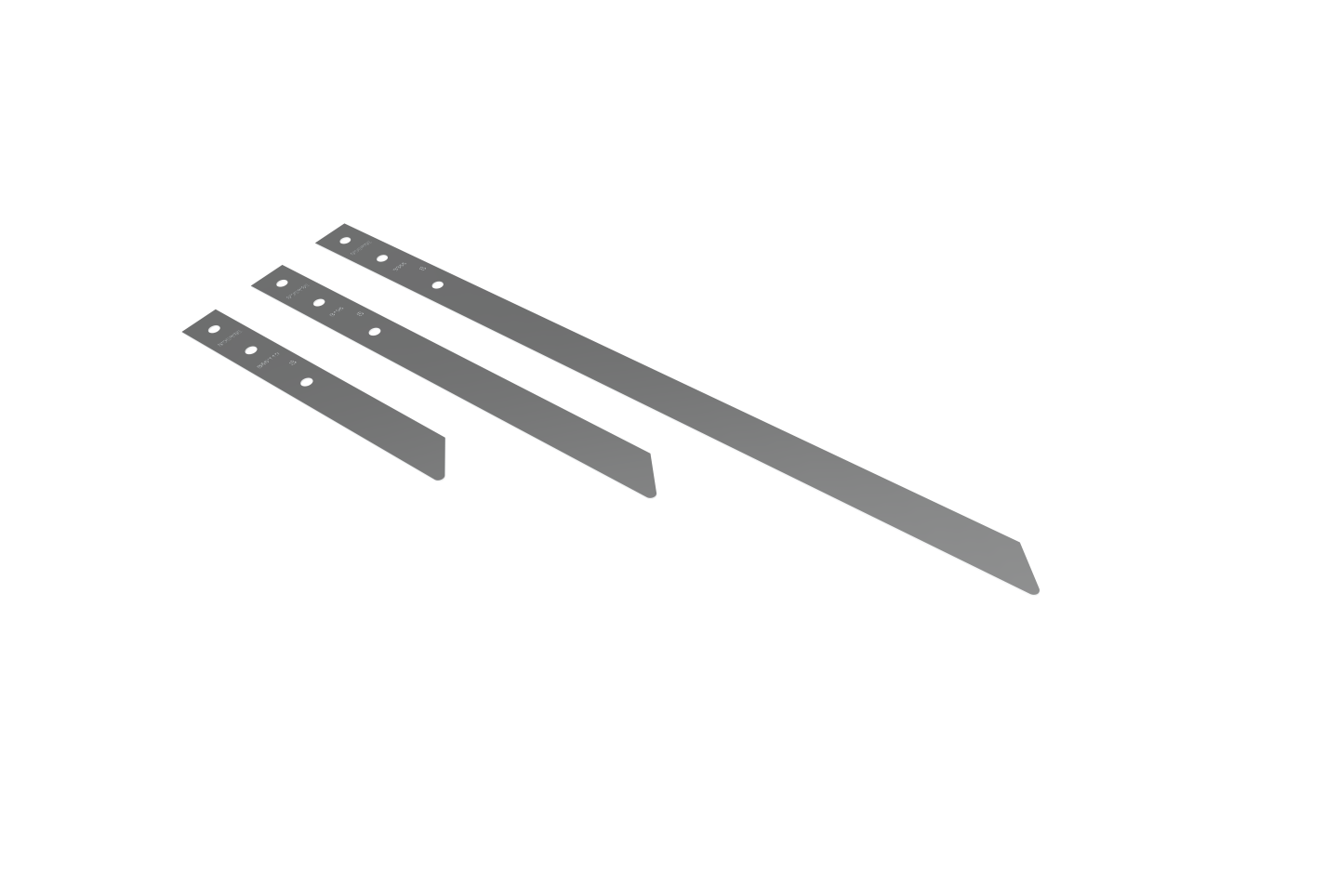
Developed for Siderise cavity barriers and firestops
Siderise B Series Fixing Bracket provides secure mechanical retention for our cavity barriers and firestops and is a requirement as part of our tested and third-party certified systems. With a 25mm width, B Series brackets are supplied in a range of lengths with three drill holes for fixing position versatility. The 7mm pre-drilled holes are designed to help facilitate a faster and simpler installation compared to brackets which require drilling onsite. To suit project specific requirements e.g. environmental conditions, our B Series Fixing Bracket is available in stainless steel (304[BC1] ) and galvanized steel (Z275) grades.
For application specific information, see technical datasheet, installation instructions and standard details on individual cavity barrier and firestop product pages.
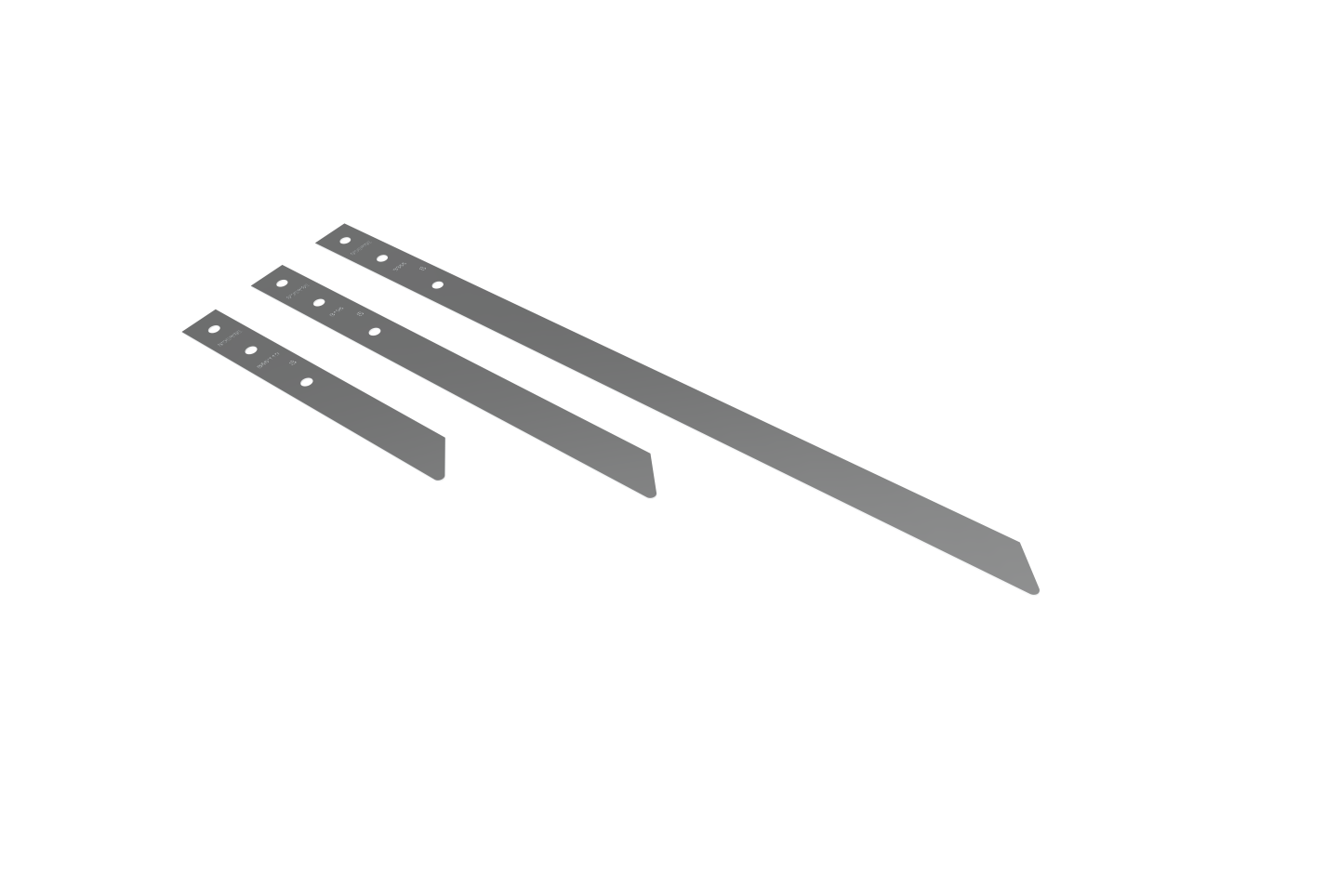
Siderise B Series brackets are designed for quick and easy installation of specified Siderise products to supported system interfaces. B series brackets are currently supplied for installation with Siderise products such as CW-FS, CW-CB, CVB, RV, CH, EW, TW, and RF. Please refer to each individual product technical datasheet and installation instructions to ascertain the correct bracket specification for the application and void dimensions on your project.
Table1: Bracket Dimensions
Product Ref. | Length(mm) | Width (mm) | Thickness Galv(mm) | Thickness SS(mm) |
---|---|---|---|---|
B65/110 | 220 | 25 | 1.0 | 0.9 |
B195 | 320 | 25 | 1.0 | 0.9 |
B355 | 505 | 25 | 1.0 | 0.9 |
Please note: Length of bracket provided is measured in flat form from tip to tip.
Table 2: Pre -Galvanised Mild Steel Properties
Properties | Value |
---|---|
Description | Pre-Galvanised Mild Steel Brackets |
Grade | DX51-D |
Coating Weight | Z275 Zinc (Min Av triple spot coating mass g/m2) |
General Characteristics | Hot Dip Galvanised giving sacrificial protection to all areas after forming and fabrication |
Dimensional Tolerances | General: ±1.00mm |±2.0º |
Table 3: Stainless Steel Grade 304 Bracket Properties
Properties | Value |
---|---|
Description | Stainless Steel Brackets |
Grade | 304 |
General Characteristics | Widely used stainless chromium-nickel steels. General purpose grades with good resistance to atmospheric corrosion and many organic and inorganic chemicals |
Dimensional Tolerances | General: ±1.00mm |±2.0º |
Note: Stainless steel 316 grade available subject to minimum order quantity. Please contact our customer service team: customer.service@siderise.com for more information.
For technical advice or support please contact: technical.services@siderise.com
For Installation Training or Site Inspections please contact: site.services@siderise.com
For technical advice or support in the Middle East, India or Asia Pacific contact: smetech@siderise.com
The information in this datasheet is believed to be accurate at the date of publication. Siderise has a policy of continuous product improvement and reserves the right to alter or amend the specifications of products without prior notice. Siderise does not accept responsibility for the consequences of using the products described outside of the recommendations within this datasheet. Expert advice should be sought where there is any doubt about the correct specification or installation of Siderise products.
Augmented Reality
Point your camera at the QR code. Tap the banner that appears on your screen.